Designing a product that tailor made to the needs of a specific environment and customer demands, requires research, learning, curiosity, and a strong desire to succeed. Lindenberg Industrial Design has all of these qualities and spurs us on to provide the best and most suitable solution.
BeeHero is just one of the many projects that required us to design the product whilst studying and learning about the environment it was to be used in. Internet research could not provide us with the information and knowledge needed. We had to make a series of field trips to gain a deeper understanding of the project’s needs and to gain practical, hands-on experience of the user’s environment. To accomplish this, we transformed a working meeting to quality time with our young son, donned a beekeeper’s outfit for a few hours. Apart from the unique experience, and Itai’s amazing hospitality, we gained an understanding of the operational restrictions involved in wearing a cumbersome beekeeper’s suit. This gave us a direction and an understanding for the design of a product that would be more suitable to the project’s needs and requirements.
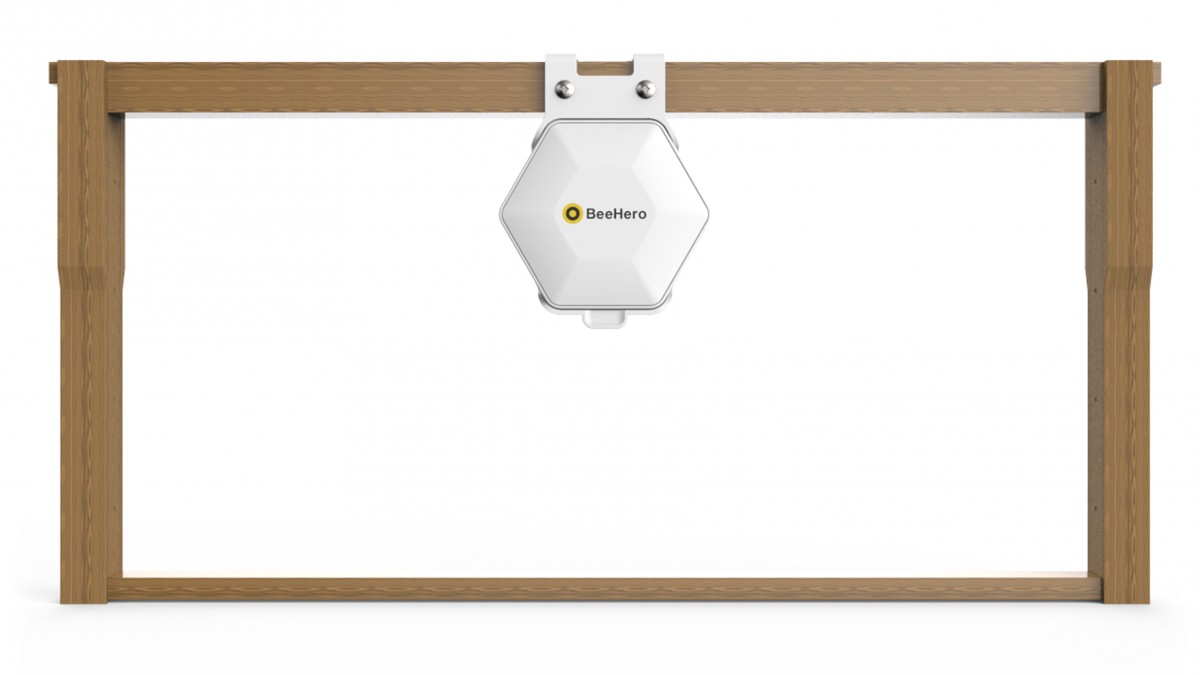
BeeHero is a smart bee sensor. That is installed in the hive and collects data which can then be used to predict the hives behavior and respond accordingly.
The central, technical requirement was to provide a sensor that could be placed inside the hive without damaging it any way and without harming the bees. The sensor needed to be easily maintained, even after prolonged use in the hive and coated with a layer of sticky honey.
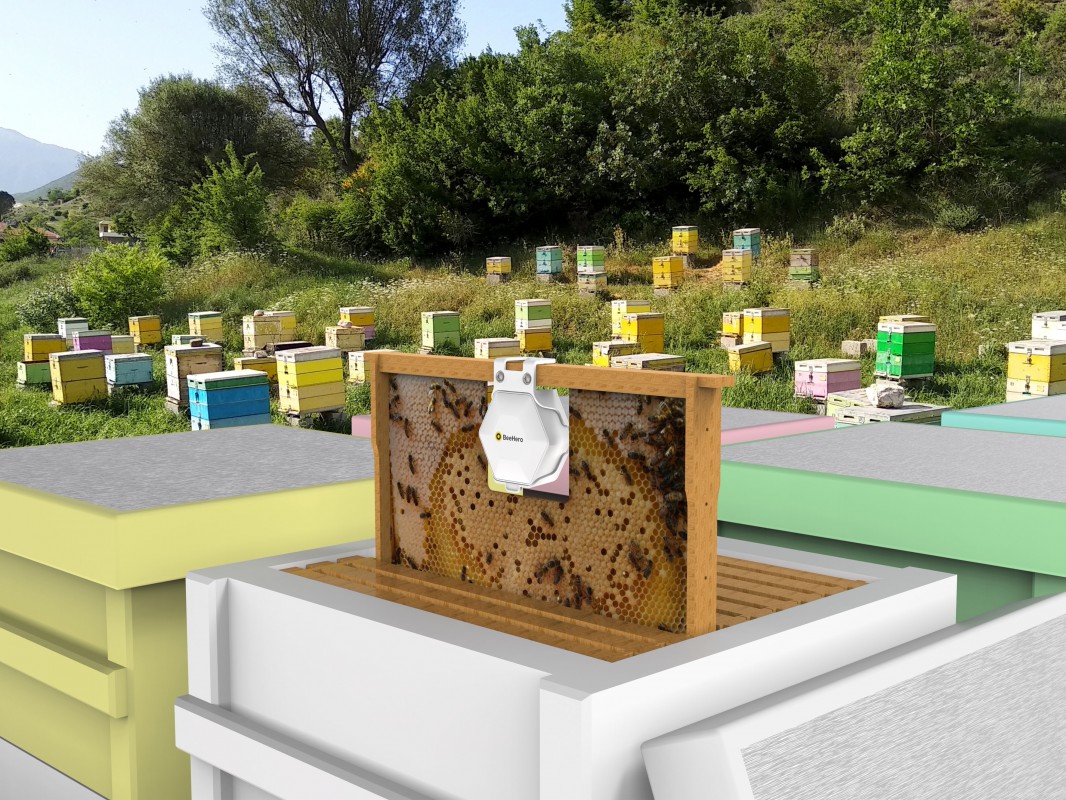
With this in mind we designed a sensor consisting of two parts: the sensor enclosure and a mounting plate. When maintenance is needed, like battery charging, cleaning, etc., it is a simple process to remove the sensor from its mounting plate, do what is needed and then replace the sensor.
A very short schedule was defined for this project. It included product design/industrial design, mechanical design, the production of functional prototypes, marketing examples and the final production design.
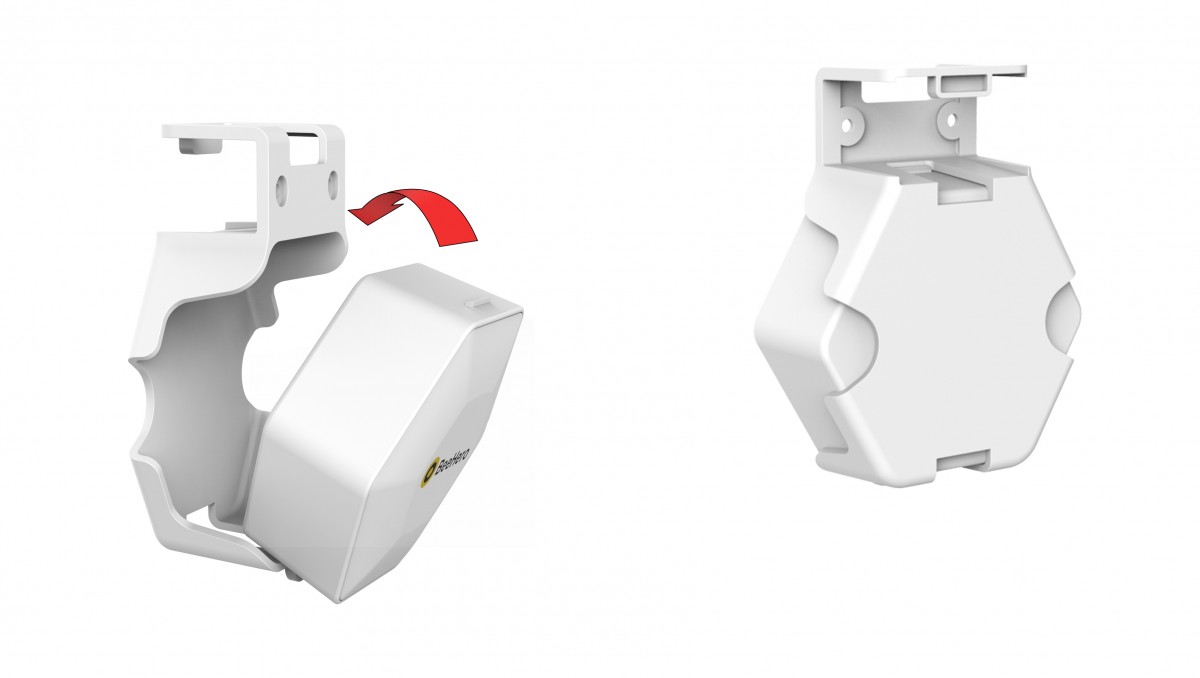
A decision was reached that would deal with all production issues, including a visit to the Chinese production facility, so that we could provide the manufacturer with rapid answers during the critical phase of the product’s first plastic injection process. During our trip to China, we also visited a silk print workshop to see the initial printing of the logo on the product. (See video)
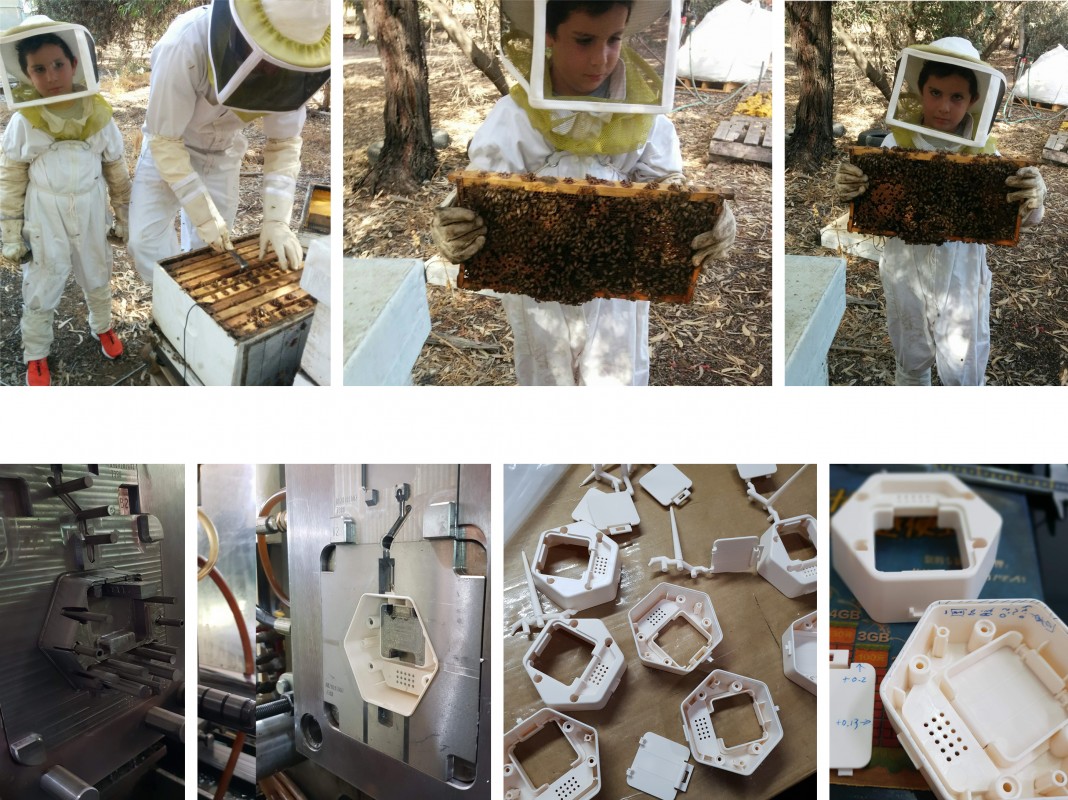
All’s well that ends well – all our hard work paid off and we delivered the first products, on time, for the pilot launch in the US.
טקסט טקסט טקסט